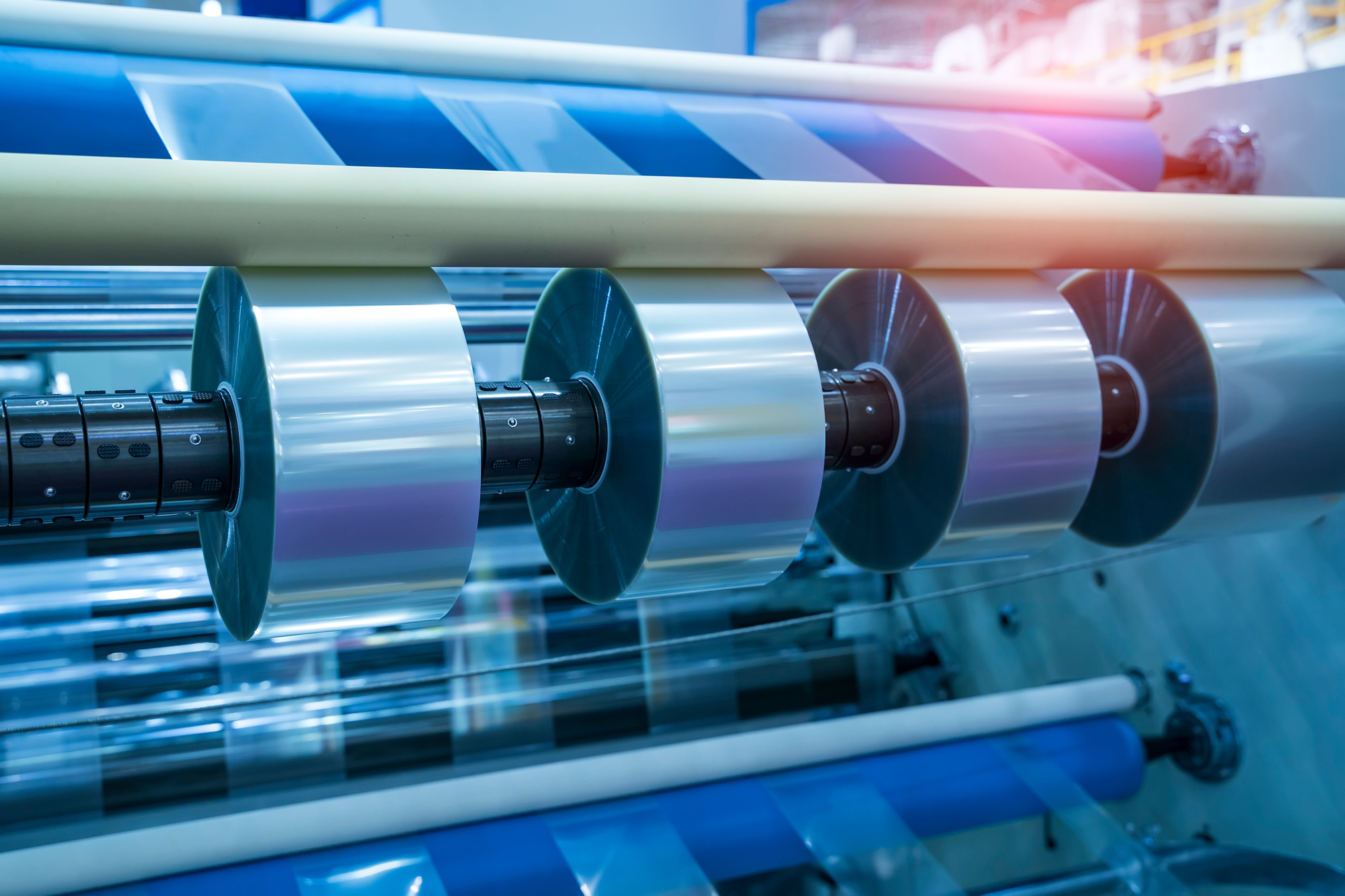
Adhesives refer to substances that join materials together through bonding. They come in many types for various domestic and industrial uses. Industrial adhesives are extremely high-strength glues leveraged in manufacturing applications and building products where robust, permanent bonds are crucial. Categories include epoxy, acrylic, polyurethane, silicone, hot melt, and light-cured adhesives. Engineers meticulously choose suitable chemical compositions depending on the materials being bonded, desired curing conditions, anticipated exposure to the environment, levels of stress, and performance requirements.
Epoxy Adhesives
Epoxies stand as one of the most common and versatile industrial adhesive types. Made from petroleum-based compounds, epoxy molecules contain epoxide rings that enable bonding through cross-linked polymer structures cured using chemical hardeners. This makes them rigid yet somewhat heat and chemical resistant while bonding tenaciously to many materials. Types include two-part epoxies, one-part epoxies, snap cure epoxies, and epoxy films or tapes.
Two-part epoxy adhesives separate resin and hardener components that only activate when mixed in precise ratios just before application. This allows flexible working times from 5 minutes up to hours to join large components. Bonding metals, composites, wood, glass, ceramics, concrete and some plastics, they cure fully at room temperature over 24-72 hours depending on the formulation. Accelerated oven curing is possible too.
One-part epoxies have resin and hardeners combined already, so no mixing is necessary. The cure process begins through a reaction with moisture in the air that plasticizes the epoxy, making one-part epoxies more finicky for open assemblies. Snap cure epoxies harness elevated heat up to 250°C to trigger near instant bonding. This suits automated production lines, bonding plastic and metal assemblies in seconds. The experts at Axiom Materials say that epoxy film adhesives act as bonding intermediaries to join uneven or curved composites and plastic parts, like in automotive interiors and airframe assemblies.
Acrylic Adhesives
Another leading category of high-performance industrial adhesives is acrylics, made by polymerizing acrylic ester monomers. Manufacturers tailor acrylics using various co-monomers and composition modifiers to optimize properties like enhanced temperature resistance, improved flexibility/elongation, or superior oil and chemical resistance depending on applications. This versatility makes them ideal for bonding an array of low-surface energy plastics, rubbers and metals while tolerating more varied operating environments.
General acrylic adhesives grip well even on uneven, porous, or contaminated surfaces, like unfinished wood and metals. The polymers link mechanically through absorbed surface layers rather than purely chemically bonding. While acrylic’s stability resists temperature, oils, and chemicals better than basic glues, epoxies still surpass them when extreme durability is paramount.
Polyurethane Adhesives
Polyurethanes (PURs) comprise another essential industrial adhesive family, formed by reacting isocyanate molecules with polyols. Adjusting those chemical ratios and using diverse di-isocyanate components means manufacturers control properties from flexibility to rigidity. Hence, the same polyurethane chemistry manifests as cushioning foam, structural insulation board, high-performance spandex fibers, and tenacious adhesives.
As adhesives, polyurethanes bond extremely well to difficult composites, rubbers, plastics, glass fibers, wood, and metals. Polyurethane glues exhibit high strength and especially excellent durability against prolonged exposure to heat, water, oils, solvents, chemicals, and weathering elements. This versatility suits them for abundant industrial and construction applications from outdoor window joining to vehicle assembly and bottom adhesives for shoes.
Conclusion
With endless adhesive type options available, engineers match substrate materials, bonding precision requirements, gap filling needs, environmental performance expectations, production speed capabilities, and regulatory compliance when selecting the appropriate chemistry for an application. Correct adhesive choices ensure strong, long-lasting bonds while mismatched glues may severely compromise product structural integrity and durability. Their unique bonding strengths plus flexibility clearly render industrial adhesives essential elements of quality manufactured goods production across sectors.